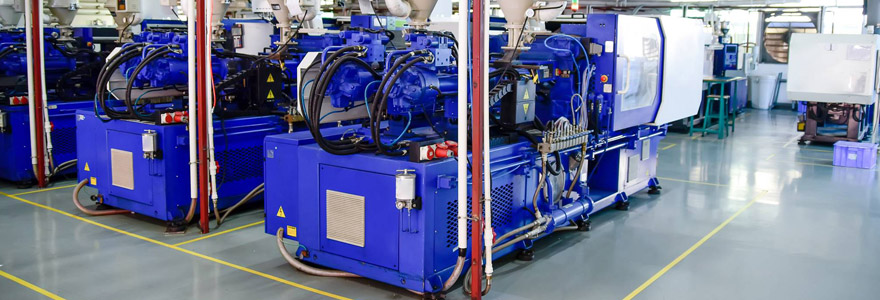
Lorsqu’on forme un objet en plastique, le processus se déroule généralement dans une machine spéciale. Le procédé se fait appeler injection plastique. Pour être plus bref, la résine synthétique ou le plastique est liquéfié par l’action de la chaleur. Son refroidissement se déroulera ensuite dans un moule dans lequel il prendra sa future forme. Focus sur les détails de ce procédé.
Injection plastique : fonctionnement de la machine
L’injection plastique peut se dérouler dans plusieurs sortes de machine. Il y a les machines :
- motorisées : activées par un servomécanisme.
- hydrauliques : fonctionnant à l’aide de moteurs hydrauliques.
- hybrides : qui réunissent, pour leur actionnement, les deux précédents systèmes (servomoteur et hydraulique).
Quel que soit le type de machine d’injection de résine synthétique, elle doit comprendre un injecteur qui mène, vers le moule injection plastique, le matériau liquéfié. Il doit également être composé d’une unité de fermeture, signalant le démarrage du moule. Grâce à l’évolution de la technologie, les matériels d’injection plastique sont devenus sophistiqués.
Les utilisateurs peuvent désormais les actionner via une commande numérique (par calculateur). Ainsi, ces derniers cris sont les facteurs d’une injection plastique à très haut débit. Cette évolution a le même principe que ces procédés voisins qui sont la conception des plaques guide-lumière d’écrans LCD, nécessitant l’action d’une machine hautement améliorée.
Si vous faites un zoom sur une de ces engins à injection plastique, vous constaterez les éléments d’actions qui sont le cylindre (fond la résine synthétique), la buse (l’administrateur), la trémie (fournisseur en matériau) et le moule injection plastique (composé de deux plaques). Pour voir plus d'information, veuillez cliquer ici jmd-cfao.com
Déroulement de l’injection plastique
Au tout début, la résine synthétique (granulée) entre par la trémie. Le procédé se suit d’une liquéfaction des pellets à l’intérieur du cylindre en guise d’élaboration de l’injection plastique. La buse envoie ensuite le matériau, en passant par un canal nommé carotte. Ce dernier vient par la suite combler le moule injection plastique à travers les tuyaux de coulée. Quand le matériau est refroidit, il se consolide également et est éjecté, une fois que le moule s’ouvre. Enfin, les bordures (non désirées) laissées par les canaux et les sections de la carotte, sur la pièce moulée, sont coupées. Notez que ces cavités coupées sont très utiles pour la fabrication de plusieurs autres produits.
C’est pourquoi vous ne devez pas hésiter à uniformiser et à remplir le moule du matériau fondu. Grâce à l’injection plastique, vous pouvez réaliser une forte production. Néanmoins, pensez à bien choisir le matériau, la moule de fabrication, et suivez bien les conditions de vitesse d’injection et de température.
Le choix de matériaux pour l'injection plastique
Le moulage par injection plastique est un procédé de formage qui utilise des moules. Un matériau, tel qu'une résine synthétique (plastique), est chauffé et fondu, puis transféré dans un moule, où il est se refroidi dans la forme que vous souhaitée. Mais qu’on est-il du choix du plastique ? Choisir des matériaux pour votre projet d'injection n'est pas facile.
À ce jour, des milliers de plastiques sont utilisés dans des applications commerciales. Il existe deux principaux types de plastiques : le plastique thermodurcissable représentant 20 % du marché et en seconde lieu le Thermoplastiques qui représentant 80 % du marché. Chaque plastique est connu pour ses propriétés mécaniques, électriques et thermiques. La fiche technique standard du matériau contient toutes ses caractéristiques, qui peuvent être mieux comprises.
Idéalement, la sélection des matières plastiques se fait en analysant toutes les contraintes liées à l'application de la pièce. Des ingénieurs rigoureux recommandent également l'analyse des modèles et des conceptions 3D. Cependant, le sens de sélection des matériaux peut être déterminé de manière simple et judicieuse. Ainsi, vous devez analyser vos besoins, ce qui est une question de poser les bonnes questions afin que le matériau plastique choisi puisse s'adapter à vos attentes.